Rural-Focused Fund Backs Maine Enterprises Tapping Technology Used In Europe
Originally posted by Forbes on February 29th, 2024
What are the chances that the first two investments of a fledgling fund focused on boosting rural economic development in the U.S. would be Maine-based enterprises using technologies with a track record in Europe, but unknown here?
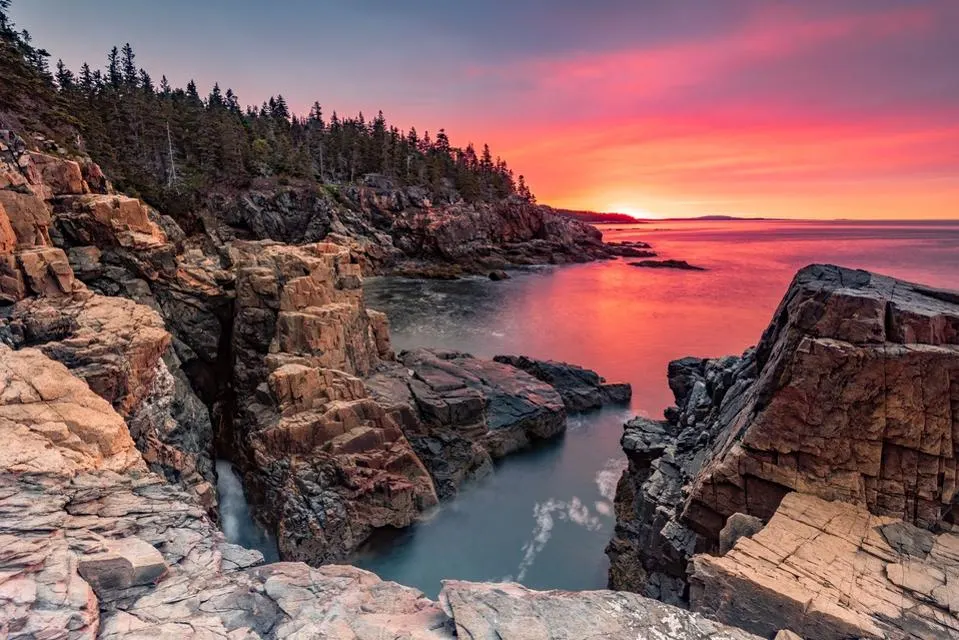
That’s the story behind RuralWorks Partners’ initial impact investments—American Unagi, which produces and processes sushi-grade American eels, and TimberHP, a maker of building insulation made of waste wood fiber.
Made in Maine Eels
With a long-time interest in aquaculture, Sara Rademaker founded Waldeboro, ME-based American Unagi in her basement in Maine about 10 years ago. Her mission: to jumpstart the growth of the domestic fish industry. After doing some research, she’d realized that eels were a perfect fish to target. ”As a little girl, I never saw myself as an eel farmer,” says Rademaker. “But this seemed like a great place to start helping the industry develop in the U.S.”
Why eels? What Rademaker learned was that, despite the rapid growth of consumer demand for sushi, the process of catching, growing, processing and selling eels in the U.S. was oddly convoluted. By law, fishermen in only a few states in the U.S. are allowed to harvest baby glass eels, and most of that activity takes place in Maine. (The eels are born near Bermuda, traveling to freshwater rivers in Maine to mature and mate). But it takes anywhere from 5 to 20 years or more for those eels to start having babies. So fisheries sell and ship the fish to aquaculture buyers in China, who raise the eels to maturity over about a two-year period in tanks. Then those adults are sold and shipped back again to the U.S., to restaurants and groceries—a highly inefficient and carbon-intensive process. “It just made no sense,” says Rademaker.
But Rademaker also found out that an already-proven technology for bringing baby eels to maturity using a recirculating aquaculture system (RAS) existed in Europe. In 2016, she started working with an aquaculture firm in the Netherlands to bring the system to the U.S.
The business started with a few tanks in Rademaker’s basement. After a few years, she moved to space at the University of Maine and started selling commercially in 2016. Then in 2022, she built a $12 million, 27,000-square-foot facility where she harvests her eels. When they’ve reached maturity, she either processes them in fillets or smoked, or sells them live, to customers ranging from three-star Michelin restaurants to take-out joints. As she scales up operations, Rademaker plans to increase production from about 15,000 pounds of eels a year to half a million.
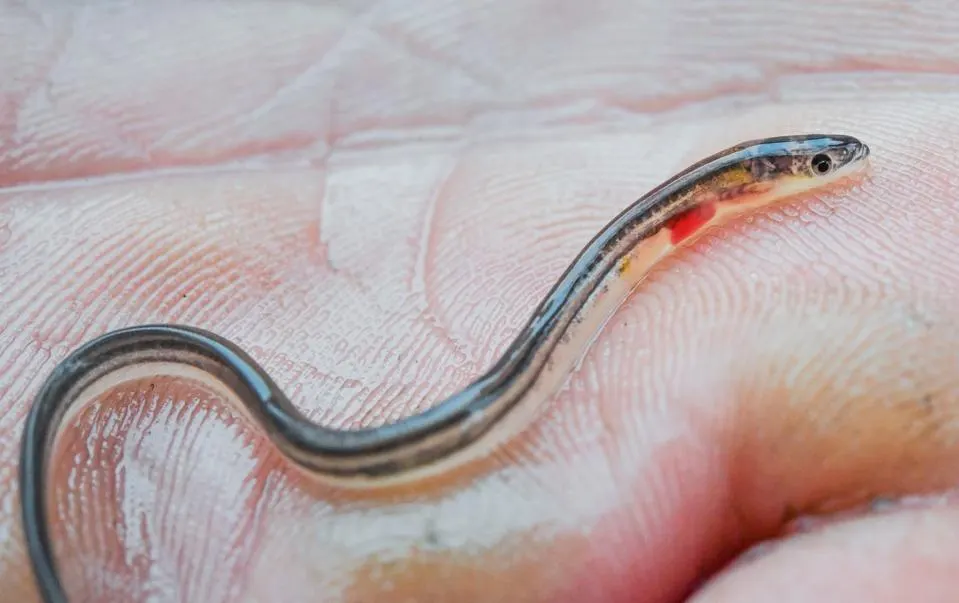
A significant portion of baby eels in the state are caught by members of the Passamaquoddy Tribe, which bought 10% of the business in 2021. The tribe is also in the process of securing a site for its own 30,000 square-foot production and processing facility that will employ about 30 tribal and community members, according to Stan Meader, CEO of Indian Township Enterprises in Princeton, ME, the economic development arm of the tribe at Indian Township.
Initially, Rademaker raised about $10 million in debt and equity from angels and others. Last year, RuralWorks invested $1.5 million and made another $1.5 million available if needed to help pay down debt, according to Skip Wyer, RuralWorks’ Chief Investment Officer.
Climate and Cost-Friendly Insulation
In a refurbished abandoned paper mill, TimberHP (the HP stands for high performance, healthy people, healthy planet) makes building insulation from waste wood fiber as an alternative to fiber glass and foam, which are not only nonrecyclable, but have a high level of embodied carbon.
Co-founders Joshua Henry, a chemistry professor at the University of Maine and a material scientist, and Matthew O’Malia, an architect building certified passive homes, met in 2015. A self-described energy nerd and environmentalist, Henry was intrigued by the potential of using wood fiber insulation to help slash carbon emissions, while also cutting energy consumption from heating and cooling systems by 90%. “Who doesn’t want to reduce the cost of their heating and cooling by that much?” he says.
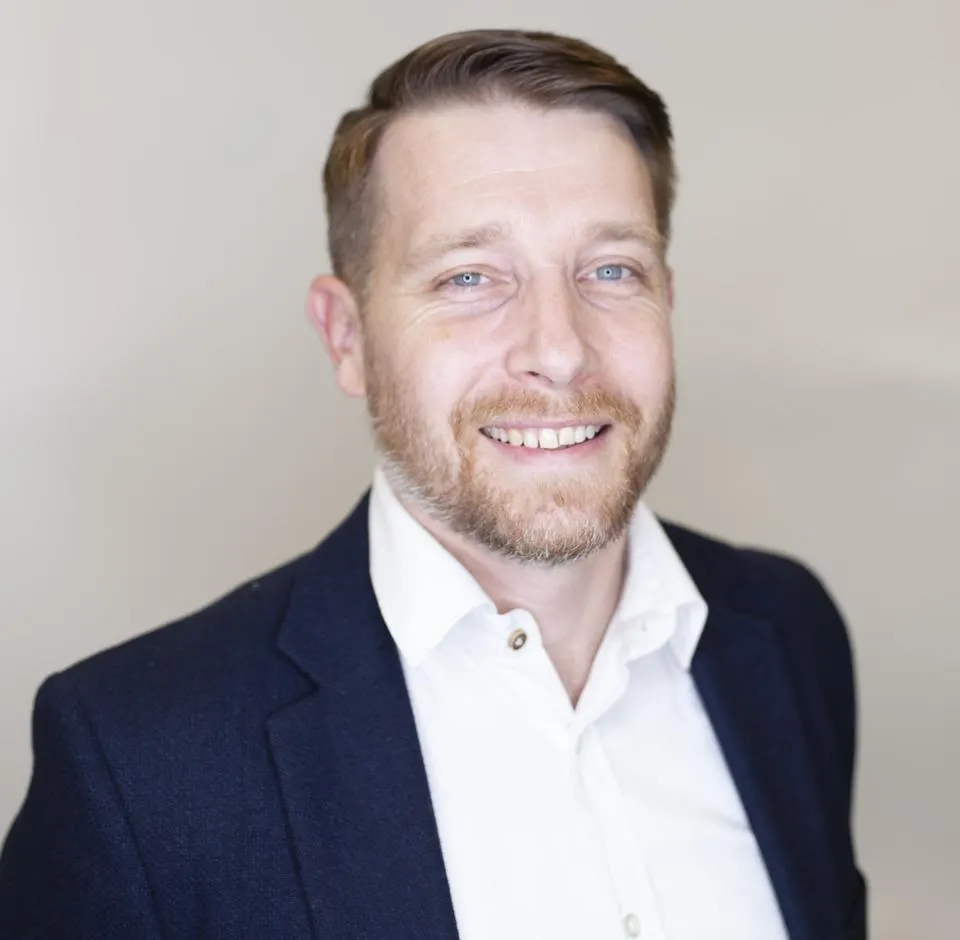
The two started collaborating and, in short order, they came across a technology in use in Europe for at least 20 years using wood fiber to make loose-fill, board and bat insulation. But, “Even though the wood feedstock in North America was at least as good as in Europe, no one was manufacturing the product here,” Henry says. A low-density, low-value product, shipping the stuff over here was prohibitively expensive.
Henry figures that one big reason for the lack of uptake in the U.S. was the 2008 housing crisis, which discouraged potential building products manufacturers from entering the market. The other: Wood product manufacturers didn’t understand the insulation market, while insulation producers didn’t get the wood products market.
Henry and O’Malia had both previously worked in Germany and spoke German. In 2017, they decided to visit manufacturers over there. Then, in 2018, one producer who was closing down his facility agreed to sell the equipment to the two partners and to help with financing the €2.5 million cost. It took six months and $4 million to disassemble the eight-story-high, 500 foot-long equipment and ship it in 150 shipping containers.
Meanwhile, Henry and O’Malia looked for abandoned paper mills that could house the equipment and become their production facility. In 2019, they found a 600,000-square-foot plant in Madison that had been used for newspaper manufacturing. Plus, a lot of the engineers who had worked there were still in the area.
It took another two years to finalize the financing. But in 2021, they closed on an $85 million tax exempt bond, with Citibank doing the underwriting, totaling their funding to about $150 million. Part of the capital stack for the bond came from a seed round of $13.5 million and a $27 million Series A round raised from about 100 investors from 2018 to 2021. More recently, they raised about $18 million through a SAFE offering; that includes $3 million from RuralWorks. Also, from 2018 to 2023, the company raised about $5 million in grants.
At the end of last year, TimberHP started up production of its loose-fill product which is sold through several large building products distributors. The second line, for bat products, started up earlier this month. The board product will launch in the late second quarter or early third quarter, according to Henry.
Launched in 2022 by Community Development Financial Institution (CDFI) Community Reinvestment Fund, USA and Conduit Capital US, RuralWorks aims to boost wealth, economic and climate resilience and jobs in rural communities by investing in growth-stage businesses with the potential to expand.